Tác giả: ThS. Đặng Thị Đan
Đơn vị: Trung tâm THM
1. Đặt vấn đề
Hiện nay, các doanh nghiệp may Việt Nam đều có qui mô vừa và nhỏ, và sản xuất hàng may mặc chủ yếu sản xuất theo hình thức gia công (CMT), luôn gặp khó khăn về thời gian giao hàng vì phụ thuộc vào nguồn nguyên phụ liệu nhập khẩu bị chậm trễ. Doanh nghiệp không đáp ứng được thời gian giao hàng, dẫn đến có doanh nghiệp bị phạt chi phí thực hiện hợp đồng. Đối với hàng may mặc, tổng thời gian sản xuất là yếu tố ảnh hưởng lớn đến quyết định đặt hàng của khách hàng. Trong khi đó nhu cầu của khách hàng đa dạng, các thương hiệu, nhà sản xuất, đơn hàng cũng phải thay đổi theo nhu cầu thực tế của khách hàng. Do vậy, thời gian sản xuất các đơn hàng trở nên ngắn và liên tục, điều này đòi hỏi các doanh nghiệp may phải thích ứng theo. Kết quả dẫn đến quá trình chuyển đổi giữa các mã hàng cũng cần thay đổi để đáp ứng được tiến độ giao hàng. Vậy để tăng được năng suất, chuyển đổi nhanh giữa các mã hàng thì các doanh nghiệp vừa và nhỏ cần có quy trình chuyển đổi nhanh ứng dụng vào triển khai rải chuyền giữa các mã hàng để nâng cao năng suất trong sản xuất may công nghiệp. Bài viết đưa ra quy trình chuyển đổi nhanh (SMED) để các doanh nghiệp có thể áp dụng vào triển khai chuyển đổi nhanh các mã hàng.
2. Khái quát về chuyển đổi nhanh
2.1. Khái quát chung về công cụ chuyển đổi nhanh
Theo tác giả Đặng Thị Tình (2020) [8] tiền thân của công cụ Chuyển đổi nhanh do Shigeo Shingo đề xuất vào năm 1955, được Toyota giới thiệu vào khoảng cuối thập niên 50, đầu thập niên 60 nhằm giảm thời gian chuyển đổi trong quá trình sản xuất từ vài giờ xuống còn 13 phút. Từ đó, họ bắt đầu tìm hiểu bí quyết đó nhưng gặp rào cản ngôn ngữ, do không có nhiều tài liệu bằng tiếng Anh. SMED (Single - Minute Exchange of Die) là thuật ngữ dùng để chỉ sự Chuyển đổi nhanh (Quick Changeover) được Shigeo Shingo phát triển vào năm 1955.
Trước khi công cụ Chuyển đổi nhanh này được nghiên cứu và phát triển, để giảm tối đa chi phí cho việc dừng máy trong suốt quá trình hoạt động, các nhà máy thường chọn giải pháp là sản xuất một lượng lớn sản phẩm nhằm đảm bảo thời gian dừng máy trên mỗi sản phẩm thấp nhất. Và các nhà máy tại thời điểm đó thường áp dụng cách tính thời gian và số lượng lô sản phẩm kế tiếp khi mà chi phí tồn kho ngang bằng với chi phí khi thiết bị dừng trong suốt quá trình chuyển đổi. Tại Toyota, họ gặp khó khăn khi áp dụng cách tính này vì chi phí tồn kho sản phẩm của họ rất cao. Cách tốt nhất để họ giảm hao phí trong sản xuất là giảm thời gian cài đặt, nếu như thời gian sản xuất giảm thì lượng sản xuất sẽ giảm, từ đó các chi phí có liên quan sẽ giảm theo.
2.2. Khái niệm chuyển đổi nhanh
Chuyển đổi nhanh (viết tắt SMED) là một công cụ của hệ thống tinh gọn Lean hỗ trợ doanh nghiệp nâng cao năng suất chất lượng, giảm thời gian chuyển đổi sản phẩm và lắp đặt thiết bị là công cụ thực hành giúp nhà sản xuất giảm thời gian chuyển đổi của một dây chuyền từ mã hàng A sang sản xuất mã hàng B [1]
3. Quy trình chuyển đổi nhanh mã hàng
Quy trình triển khai chuyển đổi nhanh mã hàng được thực hiện theo hình 1.1. Trong đó bao gồm 8 bước công việc cần thực hiện và biểu mẫu sử dụng theo dõi thời gian, năng suất trong quá trình chuyển đổi nhanh mã hàng [2]
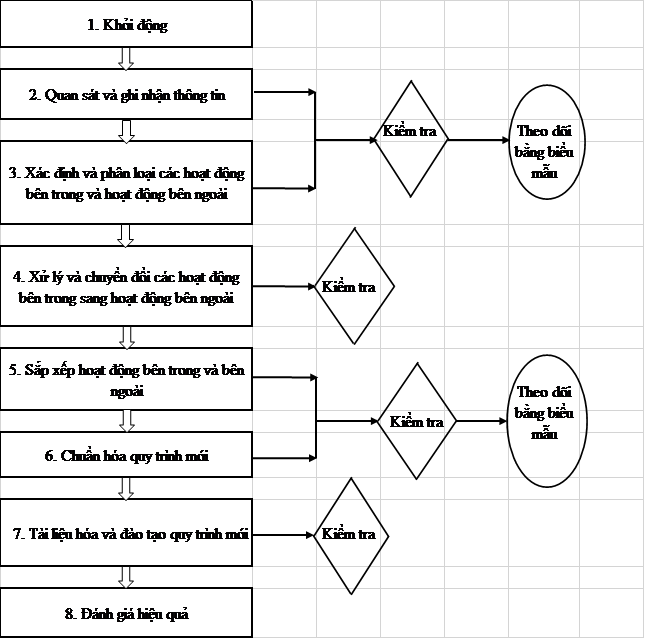
Hình 1. 1. Quy trình triển khai SMED trong sản xuất may công nghiệp[2]
Bước 1. Khởi động
- Lãnh đạo doanh nghiệp tổ chức họp đầy đủ các nhóm bộ phận liên quan đến sản xuất mã hàng để triển khai thực hiện công việc và có sự tham gia của nhân viên sau đó thành lập nhóm triển khai chuyển đổi nhanh, đưa ra kế hoạch triển khai chung cho các nhóm bộ phận gồm: Bộ kế hoạch, bộ phận kỹ thuật, bộ phận chuẩn bị thiết bị máy móc, bộ phận chuẩn bị phụ liệu, bộ phận cắt BTP... tiến hành triển khai công việc cụ thể tới từng nhóm và các nhóm lập kế hoạch triển khai công việc cụ thể theo ngày, giờ chi tiết cho từng thành viên trong nhóm.
- Thứ nhất lập kế hoạch: Các nhóm trưởng các nhóm xây dựng kế hoạch chi tiết cho nhóm của mình và cụ thể công việc đến từng thành viên trong nhóm
+ Nhóm chuẩn bị phụ liệu, rà soát và chuẩn bị đầy đủ phụ liệu đầy đủ, đòng bộ cho mã hàng như: Chỉ, khóa, mác cúc...
+ Nhóm cấp BTP: Cấp đầy đủ đồng bộ BTP đúng đơn, màu, cỡ...để cho tổ triển khai
+ Nhóm chuẩn bị sản xuất cần chuẩn bị tài liệu mã hàng, định mức NPL, giác sơ đồ, cắt BTP, làm mẫu, dưỡng...
+ Nhóm thiết bị cần lên kế hoạch chuẩn bị lắp máy móc đủ cho tổ theo kế hoạch để triển khai mã hàng từ máy 1 kim, máy vắt sổ ... và đặc biệt quan tâm chú trọng đến những máy chuyên dùng
+ Nhóm triển khai sản xuất như kỹ thuật rải chuyền, KCS cần phải thực hiện các công tác liên quan đến triển khai như: kỹ thuật rải chuyềnNghiên cứu TLKT, sử dụng thiết bị cữ gá gì giúp tăng năng suất chất lượng sản phẩm, may mẫu rải chuyền...
+ Nhóm IE làm nhiện vụ cải tiến sau khi chuyền đã triển khai ổn định sau 3 ngày thì nhóm cải tiến có trách nhiệm nghiên cứu cải tiến các công đoạn (nếu cần) như cải tiến thao tác may, vị trí đặt BTP....
- Sự cam kết của các nhóm: Mỗi nhóm và cá nhân phải chịu trách nhiệm về công việc của mình trước lãnh đạo của doanh nghiệp. Các bộ phận khi thực hiện công việc đều phải có sổ theo dõi ghi chú về vấn đề phát sinh (nếu có) trong quá trình triển khai để giải quyết kịp thời. Chính vì vậy, sự cam kết và tham gia của các nhóm và ban lãnh đạo của doanh nghiệp là rất cần thiết.
- Sự tham gia của nhân viên và phạm vi triển khai: Để ứng dụng triển khai thành công quy trình SMED cần sự tham gia của cán bộ công nhân viên trong doanh nghiệp thuộc phạm vi áp dụng như: Bộ phận kế hoạch, kỹ thuật, bộ phận NPL, tổ trưởng, KSC... Vì trong thực tế, công nhân thường nắm rõ về quy trình và công việc của mình nên hoàn toàn có thể đề xuất biện pháp cải tiến. Và trong quá trình triển khai cần họp thống nhất công việc trong ngày sẽ khuyến khích nhân viên và giúp họ tin tưởng hơn và cũng là cách để thông báo về lợi ích của các chương trình cải tiến.
- Thành lập nhóm cải tiến: Nhóm cải tiến về chuyển đổi nhanh là nhân tố quan trọng để khởi động, điều phối và giám sát các giải pháp, đề tài cải tiến gồm các đại diện của các phòng ban trong doanh nghiệp như: Lãnh đạo doanh nghiệp, kế hoạch vật tư, nhóm kỹ thuật (Tài liệu, định mức, giác sơ đồ, làm mẫu, may mẫu, nhóm cữ, gá, dưỡng, kho cấp phát NPLtổ trưởng, KCS...). Ngoài ra, để hoạt động hiệu quả, nhóm cần có những kiến thức tổng hợp để phân tích, rà soát các hoạt động sản xuất hiện tại để đề xuất các giải pháp cải tiến.
Bước 2. Quan sát thực trạng và ghi nhận thông tin
Ở bước này nhóm triển khai phối hợp với ban lãnh đạo của doanh nghiệp hoặc (người chịu trách nhiệm trực tiếp) để giới thiệu quy trình sản xuất thực tế của doanh nghiệp cho nhóm, sau đó nhóm tiến hành thực hiện theo nội dung như sau:
Thứ nhất: Quan sát thực trạng việc bố trí mặt bằng dây chuyền sản xuất, quá trình triển khai chuyển đổi mã hàng của doanh nghiệp như sắp xếp thiết bị, nơi giao, nhận BTP, vị trí đặt NPL, đặc điểm, kết cấu chủng loại sản phẩm, quy trình thực hiện, cách thức, phương pháp chuyển đổi mã hàng.
Thứ hai: Ghi nhận thực trạng quá trình trình triển khai chuyển đổi mã hàng thông qua đồng hồ bấm giờ, phỏng vấn và ghi chép tất cả hoạt động tại khu vực thuộc phạm vi áp dụng SMED như: Thu thập quy trình hướng dẫn thực hiện cho mỗi công đoạn/bộ phận, thời gian chuyển đổi mã hàng/công đoạn/bộ phận, số ca làm việc, thời gian mỗi ca, thời gian sản xuất hàng ngày, thời gian chuyển đổi mà hàng, thời gian thay đổi thiết bị, lịch giao BTP, số lượng BTP vận chuyển hàng ngày, hàng tháng, số lượng công nhân, bậc thợ ở mỗi công đoạn/bộ phận, tốc độ sản xuất của dây chuyền sau khi chuyển đổi…
Thứ ba: Xác định các dạng và tổng thời gian lãng phí của các công đoạn/bộ phận như: lãng phí vị trí đặt BTP, lãng phí về đường đi của BTP, lãng phí về công tác chuẩn bị thiết bị, tình trạng ngưng chờ lắp đặt thiết bị, BTP…trong quá trình chuyển đổi, tỷ lệ tái chế, phế phẩm… Tất cả những nội dung trên được thể hiện qua bảng phân tích thực trạng con người, thiết bị của doanh nghiệp.
Bước 3. Xác định và phân loại các hoạt động bên trong và hoạt động bên ngoài
Tại bước này, kỹ thuật quy trình kết hợp với kỹ thuật triển khai rải chuyền (chuyển đổi nhanh) mã hàng xác định rõ đâu là hoạt động bên trong, đâu là hoạt động bên ngoài của toàn bộ công đoạn của mã hàng tại doanh nghiệp may và được tổng hợp vào bảng. Ví dụ: Hoạt động “Bên ngoài” gồm những công đoạn độc lập, công đoạn đặc biệt. Hoạt động “Bên trong” là các công đoạn lắp ráp sản phẩm.
Đây là giai đoạn quan trọng nhất khi triển khai áp dụng chuyển đổi nhanh. Nếu xác định và phân biệt rõ được hai hoạt động này có thể giúp doanh nghiệp giảm 30-50% thời gian chuyển đổi sản phẩm nâng cao năng suất, cải thiện đời sống người lao động.
Bước 4. Xử lý và chuyển đổi các hoạt động bên trong sang bên ngoài
Sau khi đã xác định và phân loại được hoạt động bên trong và hoạt động bên ngoài, kỹ thuật may mẫu và kỹ thuật quy trình tiếp tục loại bỏ thao tác thừa. Thao tác thừa là thao tác không cần thiết trong quá trình hoạt động sản xuất của người lao động, hoặc sự di chuyển bất hợp lý nào đó của máy móc và không làm tăng thêm giá trị cho sản phẩm dịch vụ, và chỉ làm mất thời gian và không mang lại hiệu quả cho hoạt động sản xuất của các bộ phận/công đoạn trên dây chuyền. Ví dụ: Hành động đi lại, tìm kiếm, đi lấy nguyên vật liệu, sắp xếp công cụ, v.v. là một số lãng phí do chuyển động thừa của công nhân có thể gặp phải trong quá trình sản xuất.
Cải tiến trong: Đơn giản hóa, một số giải pháp gợi ý: cải tiến phương pháp vận chuyển công cụ dụng cụ; hướng đến tự động hóa sản xuất, v.v
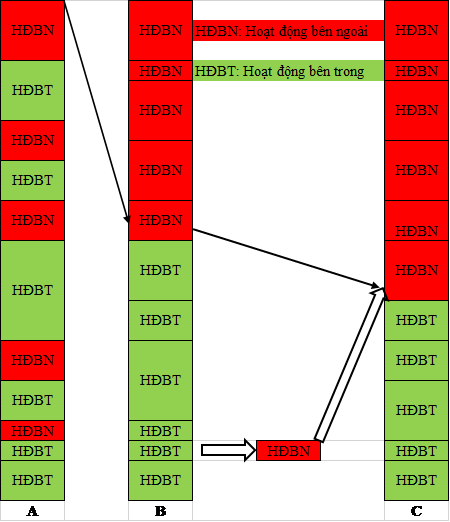
Hình 1. 2. Xử lý và chuyển đổi hoạt động bên trong sang bên ngoài
Hình 1.2 mô tả bước 3 triển khai chuyển đổi nhanh tại doanh nghiệp. Tại cột A thể hiện tình trạng doanh nghiệp khi chưa triển khai chuyển đổi nhanh có 11 công đoạn (05 công đoạn bên ngoài và 06 công đoạn bên trong). Các công đoạn tại cột A đang còn lẫn lộn giữa các hoạt động bên trong và hoạt động bên ngoài dẫn đến thời gian chuyển đổi kéo dài. Sau khi nghiên cứu, khảo sát tiến hành sắp xếp gom các hoạt động bên trong và bên ngoài vào từng khu vực và được nhận diện rõ ràng (cột B). Sau khi đã sắp xếp riêng rẽ hoạt động bên trong và hoạt động bên ngoài thì tiếp tục nghiên cứu rà lại các hoạt động bên trong (màu xanh tại cột B) và chuyển được 01 bước bên trong ra bên ngoài. Cột C thể hiện các công đoạn đã hợp lý hóa hoạt động bên trong là 05 công đoạn và bên ngoài là 06 công đoạn.
Bước 5. Sắp xếp hoạt động bên trong và bên ngoài
- Sau khi xử lý và chuyển đổi hoạt động bên trong sang bên ngoài, kỹ thuật quy trình tiếp tục sắp xếp các hoạt động bên trong và bên ngoài theo thứ tự sao cho đường đi của BTP là ngắn nhất giúp giảm thời gian tại các công đoạn/bộ phận được hiển thị tại (cột D màu xanh) hình 1.3 là giảm thời gian của 05 bước bên trong và 06 bước bên ngoài.
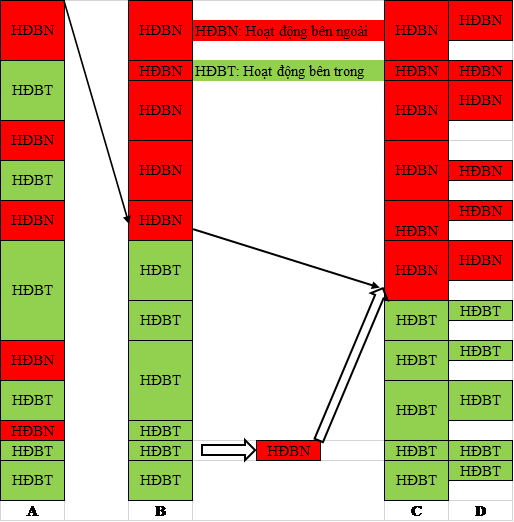
Hình 1. 3. Sắp xếp hoạt động bên trong và bên ngoài
Tại đây, kỹ thuật quy trình kết hợp tổ trưởng để bố trí lao động phù hợp với công đoạn/ bộ phận của từng công nhân. Sau đó, hai bên nghiên cứu và kiểm tra rà soát lại các công đoạn/bộ phận bên trong chuyền xem có thể chuyển tiếp được công đoạn/bộ phận nào ra bên ngoài nữa không và tổ trưởng tiến hành lập kế hoạch học việc cụ thể theo bảng 1.3 chuyển đổi mã hàng theo ngày, giờ và đầy đủ tên công nhân ứng với từng công đoạn/bộ phận của mã hàng giúp các bộ phận liên quan chủ động chuẩn bị BTP và NPL kịp thời với các hỗ trợ cần thiết như: bảng kiểm tra, kẹp file, bút chì, thước, sổ tay, tovit, kìm, dưỡng, đèn, xe đẩy, giỏ đựng BTP… cho quá trình chuyển đổi nhanh
Bước 6. Chuẩn hóa quy trình mới
Sau khi đã thực hiện 5 bước trên thì bước 6 là bước cần thiết để sẵn sàng cho việc thực hiện cải tiến (cột E). Lúc này nhóm cần cụ thể hóa các ý tưởng cải tiến cho các công việc như:
- Xây dựng và áp dụng thí điểm quy trình mới;
- Xác định lại thời gian tương ứng cửa từng bước;
- Thực hiện các điều chỉnh cần thiết (nếu cần)
- Kiểm tra và hoàn chỉnh quy trình
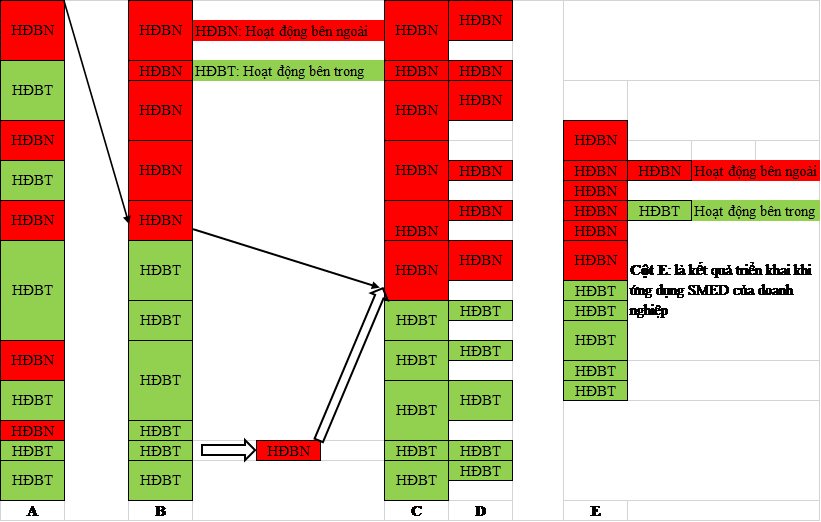
Hình 1. 4. Mô phỏng giai đoạn chuyển đổi và xử lý
Mục tiêu của việc chuẩn hóa là để các hoạt động sản xuất bên trong và bên ngoài luôn được thực hiện theo thống nhất, ngoại trừ trường hợp quy trình chuyển đổi được điều chỉnh một cách có chủ ý của khách hàng
Sau khi chuẩn hóa quy trình chuyển đổi mã hàng được thiết lập, song song với việc đó thì doanh nghiệp tiến hành:
- Phân công rải chuyền: Quản lý kỹ thuật duyệt sản phẩm mẫu của nhân viên kỹ thuật đã may. Nêu một số điểm cần lưu ý trong quá trình may mẫu, xử lý các vấn đề phát sinh (nếu có). Thống nhất quy trình ghép lao động và sơ đồ chuyền, bộ phận học việc bên ngoài, bộ phận rải chuyền bên trong. Phân công kỹ thuật đào tạo công nhân học việc và rải chuyền.
- Chuẩn bị thiết bị: Nhận thông tin các thiết bị cần dùng cho dây chuyền từ phía kỹ thuật trong quá trình may mẫu, nhận thông tin số lượng máy móc thiết bị cần dùng từ thiết kế chuyền. Chuẩn bị đầy đủ các thiết bị cữ gá lắp đặt, chỉnh sửa để sẵn sàng cho học việc và rải chuyền. Kỹ thuật kiểm tra lại toàn bộ cữ gá, máy chuyên dùng, đảm bảo các thiết bị hoạt động tốt và đầy đủ trước khi rải chuyền.
- Họp triển khai sản xuất: Các bộ phận báo cáo quá trình chuẩn bị như BTP, mẫu HDSX, phụ liệu, chuẩn bị của dây chuyển sản xuất, và một số lưu ý đặc biệt đối với mã hàng như chất lượng đối với công đoạn then chốt, treo mô hình mẫu công đoạn lên máy cho công nhân quan sát (nếu cần)…
- Rải chuyền: Đây là khâu quan trọng và cần thiết để sẵn sàng cho quá trình chuyển đổi mã hàng. Kỹ thuật triển khai chuyển đổi nhận tài liệu (đồng bộ) như TLKT, sản phẩm mẫu, bảng quy trình công nghệ, bảng màu, kế hoạch học việc… và hướng dẫn chuyển đổi các công đoạn bên ngoài (liền kề với dây chuyền đang sản xuất) và thao tác mẫu (nếu cần), tất cả các công đoạn/bộ phận của mã hàng sử dụng dưỡng/cữ/máy lập trình hoặc các công đoạn đặc biệt được quy định rất chi tiết tại bảng công nghệ sản xuất cho mã hàng. Quá trình hướng dẫn/thao tác mẫu khi chuyển đổi mã hàng cần truyền đạt rõ ràng nhằm tránh sự thiếu nhất quán và quy định sai về cách thức thực hiện một công đoạn/bộ phận và kết hợp với các biểu mẫu theo dõi thời gian trong quá trình chuyển đổi. Trong quá trình chuyển đổi này tổ trưởng chuẩn bị đầy đủ BTP của mã hàng, thông báo công đoạn/ bộ phận cho từng công nhân, bố trí cho công nhân ra học việc các công đoạn/bộ phận bên ngoài, tổ trươngt/tổ phó phải luôn theo sát quá trình đào tạo công nhân. Kiểm tra và xử lý các vấn đề phát sinh (nếu có). Rải chuyền khi mã hàng cũ còn 2 đến 3 ngày là kết thúc thì tiến hành triển khai cho công nhân học việc các công đoạn bên ngoài của mã hàng mới. Trong quá trình rải chuyền các bộ phận thực hiện lần lượt theo các nội dung sau:
+ Chuẩn bị đầy đủ bảng sơ đồ chuyền cho cơ điện, kỹ thuật và quản lý tổ
+ Chuẩn bị đầy đủ máy móc theo sơ đồ chuyền ở trạng thái sẵn sàng và bố trí ở đầu chuyền/cuối chuyền (phụ thuộc vào mô hình nhà xưởng)
+ Tổ trưởng giao chân vịt, mẫu, gá, dưỡng… cho công nhân, công nhân vệ sinh máy móc thiết bị, thay chân vịt, gá sau khi hết mã hàng cũ
+ Tổ phó giao nguyên phụ liệu mã hàng mới cho công nhân quản lý BTP công đoạn của mình
+ Cơ điện luôn có mặt trên chuyền để sắp xếp kê, cắm điện, điều chỉnh thiết bị để công nhân vào ngay vị trì làm việc
+ Tổ trưởng luôn chạy chuyền, phân công công việc, bám sát việc triển khai rải chuyền để việc triển khai rải chuyền với thời gian tối ưu nhất
+ Kỹ thuật chia theo cụm để hướng dẫn công nhân may theo dòng chảy (kết hợp các công đoạn học việc trước đó) và kiểm tra các công đoạn tiếp theo.
- Bàn giao kỹ thuật sản phẩm cuối chuyền: Sau khi hướng dẫn xong các hoạt động bên ngoài dây chuyền, kỹ thuật triển khai tiếp tục hướng dẫn các công đoạn bên trong chuyền cho đến khi sản phẩm đầu tiên ra chuyền. Sau đó bàn giao kỹ thuật sản phẩm đầu chuyền của mã hàng cho tổ theo dõi và kiểm soát chất lượng sản phẩm theo bảng kiểm tra chất lượng sản phẩm đầu chuyền: TS, QC, YCKT… Ghi nhận các sự cố về quá trình rải chuyền (nếu có) để rút kinh nghiệm và điều chỉnh. Sau đó, tổ trưởng/ kỹ thuật nhắc nhở công nhân kiểm tra chất lượng công đoạn trước và sau khi may để sản phẩm đạt chất lượng ngay từ đầu. Lập biên bản bàn giao, tổ trưởng ký duyệt và bàn giao một số bộ phận khó yêu cầu công nhân ký duyệt, quá trình kiểm tra được thực hiện như sau:
- Kiểm tra về in, thêu (nếu có): Kiểm tra về màu sắc của in, thêu, vị trí in, thêu. Kiểm tra chỉ thêu đúng màu chỉ chưa, có bị bỏ mũi, lem màu hay không
- Kiểm tra về phụ liệu: Kiểm tra xem chỉ, khóa, chốt, ore, cúc…phải đúng với TLKT và bảng màu, vị trí sử dụng đúng với YCKT, chất lượng của phụ liệu có đảm bảo theo yêu cầu.
- Kiểm tra về các công đoạn may: Đây là công đoạn chủ yếu vì có nhiều công nhân làm trên thiết bị khác nhau nên cần được kiểm tra chặt chẽ và theo một quy trình nhất định.
+ Về thông số phải đảm bảo đúng thông số kích thước và chỉ được sai lệch trong dung sai cho phép. Cách đo được căn cứ vào tiêu chuẩn hướng dẫn các vị trí đo từng chi tiết. Khi tiến hành đo tất cả các chi tiết của sản phẩm đều được để trên bàn phẳng, êm rồi tiến hành đo.
+ Kiểm tra về quy cách lắp ráp sản phẩm xem có đúng YCKT hay không như đường mí, diễu, mật độ mũi chỉ phải đều và đẹp, các đường may phải trơn đều, không nhăn, vặn, không tuột…
+ VSCN: Các sản phẩm phải được nhặt sạch chỉ, tẩy dầu (nếu có), các chi tiết của sản phẩm phải đồng màu và được là hoàn thiện theo yêu cầu của khách hàng.
Bước 7. Tài liệu hóa (chuẩn hóa tài liệu) và đào tạo quy trình mới
Chuẩn hóa tài liệu: Sau khi thực hiện các công đoạn đảm bảo đúng yêu cầu, không có vướng mắc thì nhiệm vụ của đội ngũ kỹ thuật doanh nghiệp sẽ chuẩn hóa tài liệu tạo thành các bản hướng dẫn và bộ tài liệu đó sẽ là công cụ thực hiện trong quá trình sản xuất và đào tạo quy trình mới. Các hướng dẫn trong tài liệu cần rõ ràng và chi tiết, nhưng đồng thời được trình bày thông qua hình ảnh trực quan giúp nhân viên thật dễ hiểu và liên quan mật thiết đến điều họ cần biết. Điều này rất phù hợp với các doanh nghiệp ở Việt Nam khi sử dụng các bảng hiển thị bằng hình ảnh dễ hiểu hơn so với các tài liệu văn bản. Một số công ty thậm chí áp dụng việc huấn luyện bằng phim video cho các loại công việc phức tạp hay các vấn đề liên quan về an toàn lao động.
Đào tạo quy trình mới: Sau khi đã có quy trình thực hiện chuyển đổi cho mã hàng, doanh nghiệp tiến hành đào tạo và hướng dẫn các bộ phận thực hiện theo từng bước trong quy trình chuyển đổi mã hàng và theo dõi sát sao quá trình thực hiện để các nhóm luôn được rèn luyện và nâng cao kỹ năng triển khai mã hàng cũng như nâng cao kỹ năng tay nghề của công nhân
Bước 8. Đánh giá hiệu quả
Sau khi thực hiện chuyển đổi nhanh, nhóm cải tiến thực hiện kiểm tra và đánh giá hiệu quả quá trình chuyển đổi nhanh. Và trong quá trình đánh gia có Lãnh đạo doanh nghiệp và các nhóm bộ phận liên quan như: nhóm kỹ thuật, nhóm phục vụ, tổ trưởng, KSC, IE...để họp bàn và rút kinh nghiệm mặt nào đạt và mặt nào chưa đạt để rút kinh nghiệm và khắc phục kịp thời cho lần triển khai mã hàng tiếp theo. Đây là cơ sở để doanh nghiệp quyết định nhân rộng mô hình cho các dây chuyền/ phân xưởng khác. Kết quả đánh giá cần được thể hiện bằng bảng biểu/biểu đồ…Ở bước này cần xác định các tiêu chí đánh giá như: thời gian hoàn thành công việc trước và sau khi áp dụng chuyển đổi nhanh mã hàng, quy sang thời gian cụ thể, có tính toán về kinh phí. Căn cứ vào các tiêu chí này, nhóm cải tiến tại doanh nghiệp sử dụng phương pháp so sánh để đánh giá kết quả trước và sau khi chuyển đổi nhanh và tiếp tục cải tiến (nếu cần).
4. Kết luận
Quy trình chuyển đổi nhanh có vai trò quan trọng trong sản xuất may công nghiệp, là chìa khóa quan trọng nhất để duy trì lợi nhuận, rút ngắn thời gian sản xuất, giá cả sản phẩm hợp lý, sản phẩm chất lượng tốt nhất, nơi làm việc phù hợp với xã hội và sinh thái là những xu hướng toàn cầu hóa đang nổi lên của ngành may mặc và Việt Nam cũng không ngoại lệ. Ngoài ra, quy trình chuyển đổi nhanh này còn góp phần tăng tính đoàn kết, trách nhiệm và hợp tác của các bộ phận trong quá trình làm việc. Rút ngắn thời gian chuyển đổi giữa các mã hàng trong sản xuất may công nghiệp được coi là một tham số quan trọng để bắt kịp tốc độ duy trì hoạt động sản xuất kinh doanh của các doanh nghiệp may hiện nay của Việt Nam nói riêng và của toàn cầu nói chung. Do vậy, quy trình chuyển đổi nhanh mã hàng được các doanh nghiệp ứng dụng vào quá trình chuyển đổi nhanh các mã hàng trong sản xuất may công nghiệp.
TÀI LIỆU THAM KHẢO
[1] Đặng Thị Tình (2020), Chuyển đổi nhanh-Cân bằng chuyền – Sơ đồ chuỗi giá trị, NXB Hà Nội
[2] Đặng Thị Đan (2023), “Nghiên cứu ứng dụng công cụ chuyển đổi nhanh vào rải chuyền trong sản xuất may công nghiệp”
[3] Hoàng Xuân Hiệp (2021), “Nghiên cứu, đề xuất mô hình ứng dụng Lean cho doanh nghiệp ngành may trong bối cảnh chuyển đổi theo công nghệ số”
[4] Nguyễn Khắc Oánh (2018) “Phương pháp quản lý tinh gọn Lean” Chương trình quốc gia “Nâng cao năng suất và chất lượng sản phẩm, hàng hóa của doanh nghiệp Việt nam đến năm 2020”, NXB Hồng Đức